When the floor of my home/office in Quezon city vibrated and then swirled around a bit early this week, I didn’t panic at all because I trusted the design, engineering, and construction of the building would withstand what i suspected was a pretty strong earthquake.
Although I survived the strong quake to make nervous jokes about it, my “faith” in the science and workmanship that went into the penthouse unit where I was was shaken after reading an email.
The email was sent by a friend around forty eight hours after the April 22 earthquake which emanated from Porac, Pampanga.
SUPPORT INDEPENDENT SOCIAL COMMENTARY! Subscribe to our Substack community GRP Insider to receive by email our in-depth free weekly newsletter. Opt into a paid subscription and you'll get premium insider briefs and insights from us. Subscribe to our Substack newsletter, GRP Insider! Learn more |
I’ve known this friend of mine for years now and not once has my friend sent me a bum steer. So I gave the two documents emailed to me a thorough read and knowing a little about steel, I realized the dire implications of what the documents were saying.
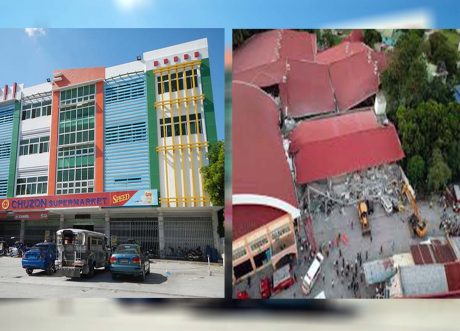
Collapsed. Chuzon supermarket turned to rubble by the 6.1 earthquake that hit Porac on April 22. Government officials have hinted at structural and construction flaws as the cause of the collapse of the structure, killing 7 people and injuring more than a dozen people.
Before showing you what the document says, let me first say that I believe engineers, builders, and land developers here in the Philippines would not knowingly endanger the lives of millions of Filipinos.
Moreover, they may be well aware of certain practices of construction material suppliers and have accounted for it using a variety of means. Although I do not know it for a fact, but I assume that they have their own ways of testing the materials they use in constructing high rise buildings and have executed their designs knowing exactly the sorts of stresses that their materials can withstand.
Now, on to content of the email…
It basically argues that government regulators have been using a standard for steel used in the construction of high rise buildings that other countries around the Pacific Ring of Fire have junked in favor of standards that they claim are superior.
Here is an excerpt from the email which makes reference to a senate hearing last year:
The hearing tackled the issue on the mislabeling of the quality grade of the steels that are locally produced. Quench tempered (QT) steels are made with softer cores, and the outside coating is hardened during the temping process; this is done by spraying water on the heat-tempered steel to toughen the coating. But unfortunately, the standards of testing steel in the Philippines are not as thorough, and a product that is made with grade 40 steel could pass as grade 60 because of the quench tempered coating.
The second hearing, dated September 11, 2018, pressed more on the issue of the mislabeling, plus emphasis on the discussion of the effects of the use of QT bars in the construction of high-rise buildings.
The hearing also touched on Engr. Morales’ findings on the effects of the QT steel used in high-rise construction. Some 10 years ago, Pagasa Steel (name not quoted in hearing notes) questioned Steel Asia’s use of the new method of quench tempering steel; at the time, micro alloyed steel bars were prominently produced and used. They wanted to give the new process a bad taste in the mouth, and urged Morales to do research on the situation.
Backed with funding from Pagasa, Morales penned a research piece “A Clear and Present Danger – The Use of QT or TMT Rebars in Seismic Zone 4”, it states that there is a danger with the use of the bars in question in areas surrounding the Pacific Ring, and where earthquakes can go up high in magnitude numbers.
As mentioned above, steel rebars in the Philippines are only tested for tensile strength, which is not an accurate measure of durability and toughness when faced in high magnitude conditions. A cyclic loading test can provide a much more accurate account, which puts the steel under multiple cycles of pressure to determine withstanding strength, but unfortunately is not a practice used in the Philippines.
Moreover, out of 195 countries, 5 have banned/discontinued the use of quench tempering high-grade steel. These countries are Japan, Taiwan, New Zealand, Canada and the US. Most of these countries are near the Pacific Ring / seismic faults.
If you are like me and wondering what steel rebar is, this page from Design Buildings Wiki may be sufficient for getting some idea:
Rebar, also known as reinforcement steel and reinforcing steel, is a steel bar or mesh of steel wires used in reinforced concrete and masonry structures to strengthen and hold the concrete in tension. To improve the quality of the bond with the concrete, the surface of rebar is often patterned.
Rebar is necessary to compensate for the fact that whilst concrete is strong in compression, it is relatively weak in tension. By casting rebar into concrete, it is able to carry tensile loads and so increase overall strength.
Different uses of rebar include:
- Primary reinforcement: Used to provide resistance to support design loads.
- Secondary reinforcement: Used for durability and aesthetic purposes by providing localised resistance to limit cracking and temperature-induced stresses.
- Provide resistance to concentrated loads, spreading it through a wider area.
- Assist other steel bars in accommodating their loads by holding them in the correct position.
- External steel tie bars to constrain and reinforce masonry structures, sometimes as a means of building conservation.
- Reinforced masonry: Some masonry blocks and bricks include voids to accommodate rebar to carry tensile loads. The rebar is secured in place using grout.
The email goes on to say that the problem is not Quench Tempering itself, but alleges that the steel from PISI (an association of Steel companies for high rise infrastructures) has grade 40 core material which can pass grade 60 after QT.
Although not completely grade 60, it is alleged that they are sold as grade 60. It also claims that 50% of steel in PH comes from company that practices mislabeling and conjectures that 50 percent of buildings in the country are at risk.
Assuming that this is true or even partly true, shouldn’t the government find out if buildings have this mislabeled steel and if so, determine the measures that must be undertaken to reduce the risk of a catastrophic collapse of these structures WHEN the next earthquake hits.
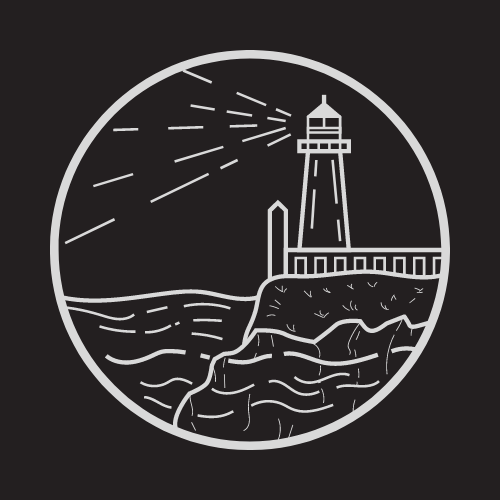
Writer.
Just for elaboration, when you are undergoing a construction project here in the Philippines, you will of course need a structural engineer to design accordingly your requirements. They will specify the strength of both concrete and steel. For concrete, they will indicate the psi requirements while for steel the grade required, be it Grade 40 or Grade 60. This is for the design part.
Also, prior to actually designing the building, a soil test is required to be done if you are a 3 storey structure or higher. If the soil test report is properly (or even actually done), it will detail the seismic zone considerations for the structural design as well as the depth required to achieve the proper strength of soil required below the footing/foundation. Report will also have recommendations as to the type of foundation the structural engineer may explore, subject to their own analysis and review of the final building requirements.
Now during construction, your steel will be ordered, either by the builder/owner or contractor (depending on the terms of their agreement as to who delivers what). Usually, if you order straight from the manufacturer, you will get a mill certificate for the steel and for the concrete, you will see it in the receipt of the delivery (this applies to ready mix concrete and not those one bag cement mix done by smaller construction projects).
But the testing and checking is not just reliant on the receipts or paperwork from the supplier. Under normal circumstances, even with the supplier guarantee of the delivery made is to spec, it is required to had them tested by a laboratory whether or not they are up to specs of what was ordered. For concrete, testing of samples (usually they look like “mohon” or concrete cylinders) are tested at 7 days, 14 days, 21 and 28 days if they are achieving the strength as required by the design. Sometimes, curing can be faster than the maximum 28 day interval, but it should not take longer than 28 days.
For steel, it is the same. There will be random sampling where cuts of about 2 to 3 feet will be taken from the batch delivered and sent to the laboratory for tensile testing and the product specifics as claimed will be written on one side and on the other side will be the as tested results. You will easily be able to confirm whether it is a pass or fail.
All these testing of materials results should be attachments when you submit your documentation for occupancy permit application.
Regarding the 4 Storey Structure that collapsed in Pampanga, the questions need to start with the following:
1) What was applied in Building Permit and Occupancy Permit? There is currently a rumor it was only supposed to be a 2storey structure? I don’t know where this rumor started but it has been said in the news once or twice. Not verified, but still. That is easy to trace back official records from the Building Official.
2) Since it is a 4 storey building, where is the soil test report? What does it require? Per news reports, the area is predominantly covered by lahar, basically, the natural grade line is “below” the current grade line. At 4 storeys, it is highly unlikely for lahar (loose) to be able to provide sufficient Soil Bearing Capacity and the Soil Test report should vouch for whether or not there is enough stable soil to get the required bearing capacity for a 4 storey structure.
3) What were the attachments to the “logbook” upon completion of construction and submitted reports of material testing should be there as required prior to obtaining an occupancy permit, which is a prerequisite before you are even able to apply for a business permit to operate/occupy the building.
These are all just records that can be checked by building official to trace back the history of what was… then should they be in order, they can now compare what it is to what it should be as reported to them.
That’s what I see and I find odd that the records have not been retrieved yet.
And what did the owner say since he is in custody? He should have a copy of his own building permit plans (with stamps as received by the building official) as well as “as built” plans (as completed by his contractor along with any warranties).
Thanks for the above comments. It is an excellent detailed information. We need honest Quality Assurance Testers, on site and in the laboratory.
Qulity Assurance Testers must not compromise the lives of people. Our country sits on the Pacific Ring of Fire…
I’m glad to have giving some enlightenment on some procedures/steps in the process.
Regarding the issue of Quenched Tempered (QT) Steel, this has been an issue we have been somewhat aware of in the construction industry. I have asked some contractors and structural engineers about it.
Based on what I was told, QT is not really allowed to be used if you are over 2 storeys or in high seismic zones. That would mean your site/lot is possible close to a fault line or ground stability during seismic movement/distortion. The Seismic Factor is included in the soil test report and is part of consideration of your structural engineer when designing the building as well. I think it is “N” Factor (if I’m not mistaken).
Your architect and structural engineer will really need to see that report to not only for design consideration but also for Projected Construction Cost Estimates. Without good data to start with, no designer will be able to give the correct output, and the dominoes will start to fall from there.
I’d like to add though that Soil Test Reports are not under the design team’s scope of work and under the owner’s duty to provide his selected design team. Granted, the owner will most likely not know what due diligence is required of him so that is why he needs his consultants to inform him of these things. Whether he does it, is another question entirely.
The safety of the people shall be the highest law, observing all the safety rules that had been written in the blood of less careful men.
Dear Mr Farol,
While I agree with most of YOUR commentS, I wish to clarify that I have NOT RECEIVED ANY FUNDING OR BACKING TO PUBLISHER MY PAPER
‘
The Research was done as part of my duty as a Member of th BPS TECHNICAL COMMITTEE ON LONGS ( REBARS) .
Thank you
Emilio Morales CE MSCE